Toothpaste tube is a common packaging container, its main material is plastic, commonly used are polyethylene (PE) and polypropylene (PP). Toothpaste tube forming process is divided into two methods: injection molding and extrusion molding, among which extrusion molding is more widely used. This article will focus on the manufacturing process of toothpaste tube by extrusion molding.
“Overview of Toothpaste Tube Forming Process”
Ⅰ.Raw material preparation
1.Plastic particles: Choose corresponding polyethylene or polypropylene particles according to different requirements.
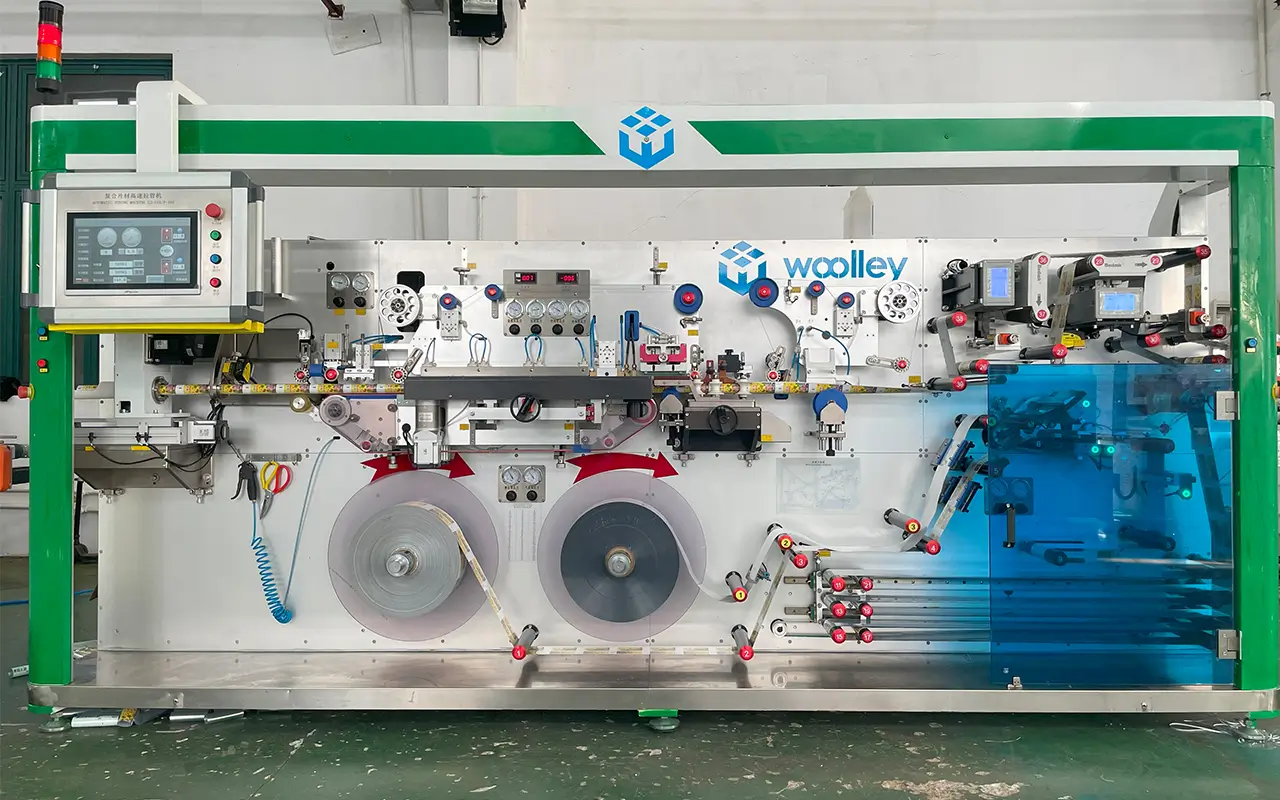
2.Additives: such as pigments, stabilizers, antioxidants, etc. Pigment
3.Lubricant: zinc stearate or sodium stearate can be selected.
Ⅱ.Extruder
1.Put the prepared plastic granules into the extruder and add appropriate amount of additives and lubricants.
2.Adjust the temperature, pressure and speed of the extruder to achieve the best state.
3.Start extrusion molding. The pre-treated plastic granules are put into the heating barrel through the screw, melted under high temperature and high pressure, and then extruded through the die head.
4.Cut the extruded plastic tube into the required length and cool it
Ⅲ.Tube shoulder forming
Wollley JX-HS70 can be used to form shoulders, threads, and holes in one step, with beautiful appearance and no sprue. All kinds of heads on the market can be formed. Flat tubes, lipstick tubes, and large-diameter tubes can also be made. One machine solves most of the shoulder injection problems and is super cost-effective.
Ⅳ. Printing machine
The shoulder-molded tube is sent to the printing machine for printing. Woolley has two types of offset printing machines for you to choose from: 6-color and 8-color. At the same time, Woolley also provides screen printing machines and hot stamping machines.Ⅴ.Top sealing and capping
The printed toothpaste tubes are sent to the assembly line to install parts such as caps and seals.
Ⅵ. Quality Control
1.Plastic particles should comply with relevant national standards, and various additives and lubricants should be added in strict proportion. 2.The extruder should be operated in strict accordance with the operating procedures to ensure the stability of parameters such as temperature and pressure. 3.The toothpaste tube forming machine should adjust the appropriate temperature and pressure to ensure stable product quality. 4.Each batch of products must be tested, including appearance, size, capacity and other aspects.Ⅶ.Summary
The toothpaste tube molding process is a delicate and complex process that requires strict operation and quality control. By optimizing the process flow and improving the accuracy of the equipment, high-quality toothpaste tube products can be produced. The fully automatic PE tube production line produced by Woolley can meet the various production needs of customers. At the same time, we also provide customized machines. Welcome to consult with the manufacturer.